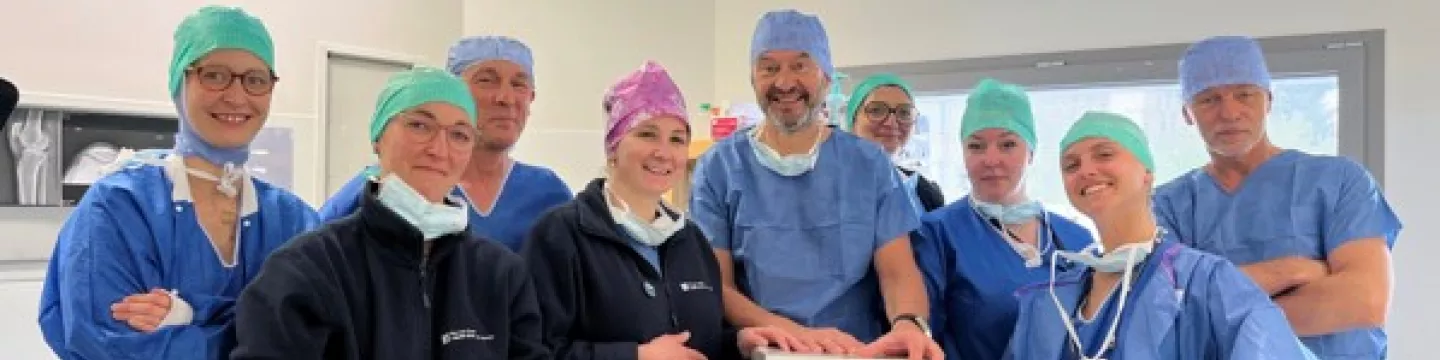
Innovation Award nominée tailor-makes knee implants
" Every year, 2.6 million patients around the world have their arthritic knee joint replaced by a knee prosthesis. After the surgery, up to 20% of the patients still have pain or stiffness, because of difficulties in fitting the implant to the native bone. Doctors in Ramsay Santé private hospital Jean Mermoz, developed a new technological process to tailor these implants. The goal is to increase the number of very satisfied patients and to restore patients’ function so that the knee “works like before”.  "
The Lyon School of Knee Surgery is the cradle of orthopedic surgery in France, with a steady connection between the industry and academics. The hip prostheses developed also in Lyon in the 1980s and are still world references, and the town is still proving its traditions.
The private hospital Jean Mermoz, built in 2008, is with its 330 beds and 27 operating rooms a flagship hospital of Ramsay Santé. Here, shoulders, spines, hips, and knees are fixed – and numerous football players have been treated in these operating rooms. Every year, more than 1000 patients have a hip or knee prosthesis implanted at Jean Mermoz.
Dr Michel Bonnin is an orthopedic surgeon who has been operating at Mermoz since it opened in 2008. He is an active researcher with a PhD, which gives him a scientific approach to his everyday mission to help orthopedic patients.
He explains how orthopedic surgery is often about finding workarounds. When it comes to knees, each patient has its own unique anatomy. Even though there are joint prostheses available in many different sizes (filling up the storage rooms at the clinics), the surgeon still needs to adjust the implant to these individual conditions. Moving a ligament here, restoring some anatomy there... It can be both challenging and fun, but the results of the procedures are very surgeon-dependent. Up to 20% of the patients are not satisfied and are forced to live with continued pain or stiffness after the surgery.
Ideas of a tailor-made knee implant
“When we began the project 10 years ago with my partner Dr Tarik Ait Si Selmi, we were just looking for a way to perform anatomically better surgeries”, Dr Bonnin says. Instead of just offering different sizes, they wanted to tailor the implants. The idea was to perform a CT-scan of the patient’s joint, then use the picture together with a software program to create a unique product for each patient’s needs. First, they tried 3D-printed implants. Since the quality was not good enough, they tried robot-operated metal machining instead. And voilà – the “Origin” knee implants were born! The product was a tailor-made solution for each patient, according to their individual knee anatomy: A specific implant with the dedicated tools and cutting guides in a single box.
pic solution
To analyze the benefits of using these implants, a scientific study was planned and carried out. Ramsay Santé was an enthusiastic partner for the study, providing both economical sponsorship and valuable help with the scientific work from Dr. Stephane Locret.
The project started in 2013, and the process was standardized and CE-marked in 2018. The medical team tried partnering with different companies before they landed with the Swiss company Symbios. “It takes time to be completely sure” explains Dr Bonnin. We needed to be sure before marketing the “Origin”.
Now, they have been using tailor-made knee implants routinely since January 2018. For each operation, the set of the sterilized implant and instrument is delivered in a single small box to the hospital a few days before the scheduled surgery. This reduces the burden of logistics and storage.
Since the bone-implant fit is better, the need for extra procedures during the surgery is reduced, and the operations are faster to perform. It also leads to shorter downtime between operations, which allows more efficient utilization of the OR and time of the surgical team. According to the scientific evaluations (evidence level IV), the recovery of knee function is faster, clinical scores at 1 and 2 years postoperatively are better, and the “personal alignment” is better preserved. Also, the patients report greater rates of satisfaction. With the old method, 50-55% of the patients were very satisfied, now this has significantly improved to 65-70% (results to be published).
Personalized medicine technologies together with good preoperative planning, seem to work out fine. But to start using it more widely, this new method must not be more expensive than today’s solutions. So, is it?
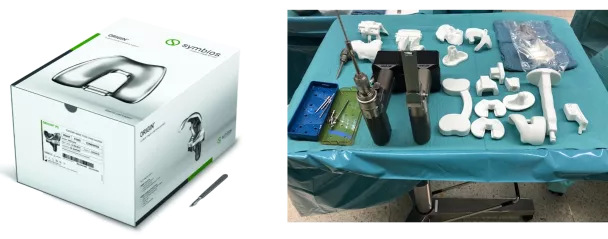
Effects on workflow, stress, and education
The team has also found a few unexpected non-medical benefits.
The stocks in the storage rooms got smaller, which is believed to lower the costs. A medico-economic study to evaluate the cost reduction is being performed, but there is no data yet.
The workflow, and thus the working environment, improved for the surgeons and scrub nurses, who arrive in the operating room at 6 am. Since the instruments are patient-specific and single-use, each operation now requires far fewer tools. The time to arrange the instruments gets shorter, with less stress of handling bulky and heavy trays between operations. “The nurses love that!”, says Dr. Bonnin. “Before, it only took one soft paper tear in the sterilized goods to cut the workflow of the OR. Now there is one box, one tool, and those risks are lowered.”
From an educational perspective, it has become easier for the nursing staff who needed less training when a new implant or instrument set was introduced. When the procedure was simplified, it also benefited the young surgeons, learning the procedure. “They just follow the protocol, and the learning has gone from complex to easy – this is simply magic,” says Dr. Bonnin. But it also helps more experienced surgeons. “The move from craftsmanship to standardized procedures is now reaching a tipping point. This is a quality question”, he highlights.
The next steps
Dr. Bonnin claims that in ten years, all knee implants will be tailor-made. Why? Obviously for the quality part, but also because this is the solution to a supply chain problem that all orthopedic surgery units are aware of. “It’s impossible to keep a sufficient stock. We often used to get messages from the supplier that “we are out of size 4 knee or 10 hip” and had to postpone planned surgeries. Nobody liked that. Neither the patients nor us surgeons.” Now, there are no delays or cancellations due to the unavailability or unreadiness of sterilized sets of instruments. It is highly likely that this paradigm shift will also benefit emerging countries with fewer surgeons.
But now the future is here, and big players are interested in this true patient-centered success. By improving the process, the concept of tailor-made implants has the potential to revolutionize knee implant surgeries. Dr. Bonnin is proud that he and his team have been able to convince the surgical community, the hospital, and the manufacturer that this is the best concept. Strong partnerships and local synergies are needed when changing a paradigm with revolutionary procedures.
“To us, this was never an economic endeavor. We just wanted to solve the real problem. We spend our life implanting knee prostheses. Our goal was just to improve the process, to improve daily activities of surgeons” Dr. Bonnin concludes
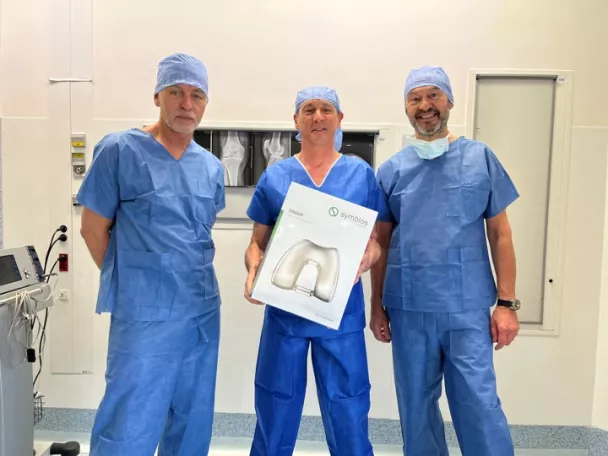
" Every year, 2.6 million patients around the world have their arthritic knee joint replaced by a knee prosthesis. After the surgery, up to 20% of the patients still have pain or stiffness, because of difficulties in fitting the implant to the native bone. Doctors in Ramsay Santé private hospital Jean Mermoz, developed a new technological process to tailor these implants. The goal is to increase the number of very satisfied patients and to restore patients’ function so that the knee “works like before”.  "